Brochure
Download our document to see specific data of the service and how we work.
Let’s Start Work
Together
Please feel free to contact us. We will get back to you with 1-2 business days. Or just call us now.
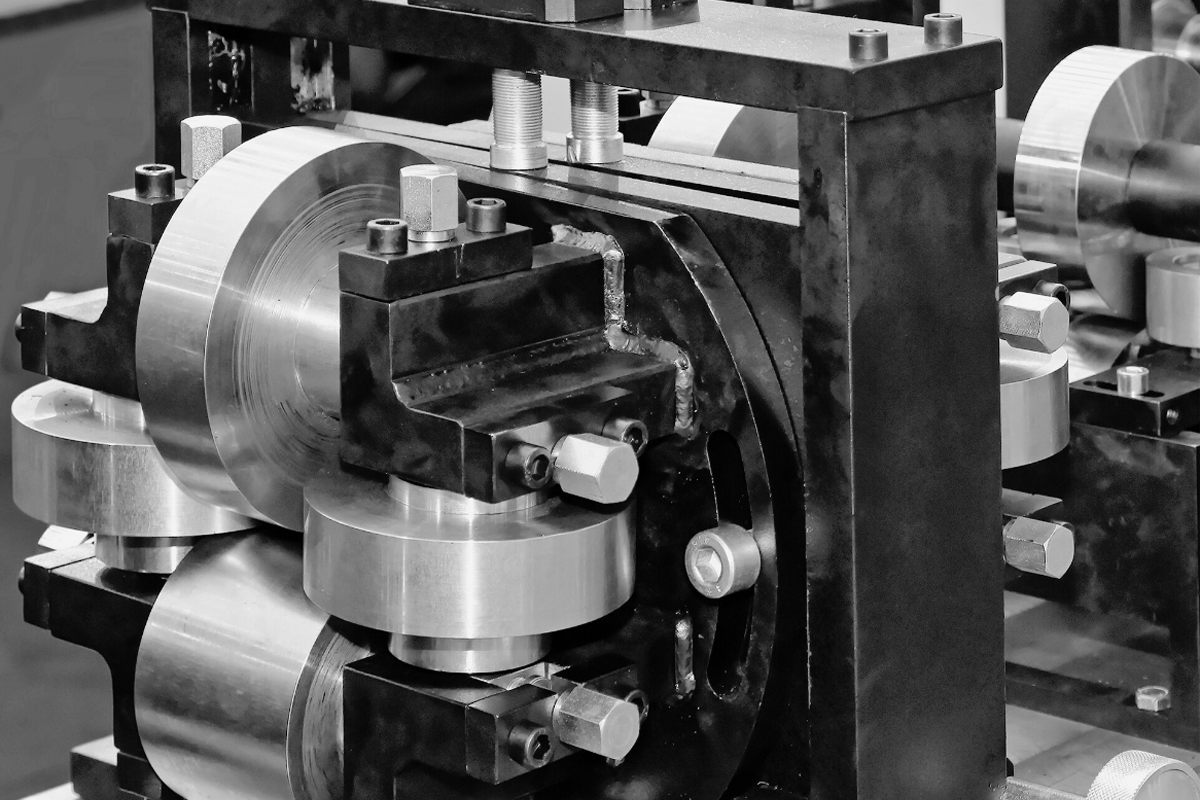
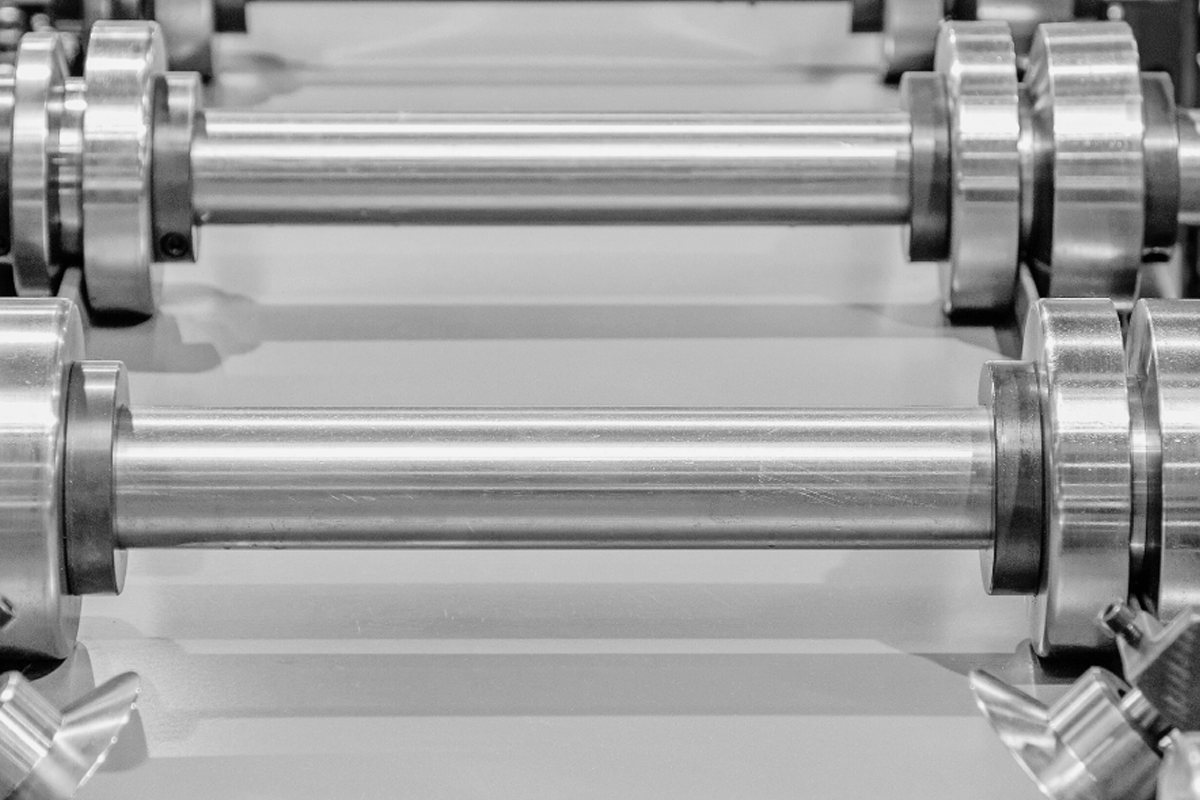
Cold Roll Forming - An Overview
Cold Roll Forming is a continuous process that utilizes a series of paired roll tools to progressively shape a flat strip of metal into the desired profile. This process, known as ‘Flowering,’ involves gradual changes in the shape of the strip as it passes through different stages.
Cold Roll Forming offers several advantages over other production methods. As a continuous process, it eliminates the need for stage production, finishing, and sub-assembly operations. This method is extremely accurate and highly efficient, making it ideal for forming profiles in large quantities.
Our Solutions & Benefits
Cold Roll Formed products are widely used across various industries and continue to find new applications daily. They have replaced many conventional methods, offering significant improvements.
- Complex Geometrical Shapes: Ability to produce intricate shapes.
- Consistency and Accuracy: Achieves better consistency and precision.
- Versatility: Suitable for varying thicknesses and lengths.
- Increased Strength: Strain hardening enhances strength.
- Lightweight and Rigid: Saves material and reduces costs.
- Integrated Secondary Operations: Combines multiple processes, speeding up production.
- Material Compatibility: Can form both ferrous and non-ferrous metals.
- Coating Flexibility: Eliminates secondary coating needs with galvanized, vinyl-coated, or plastic-enclosed metals.
- Enhanced Manageability: Improves handling.
- Maximum Straightness: Ensures straightness.
- Closer Tolerances: Maintains tight tolerances.
- Superior Surface Finish: Provides a better finish.
For the roll forming, dynamic simulation software being able to understand the different stress that will be introduce into the material during each pass through a roll former and therefore being able to make the correct adjustment to the design of the roll, all without having to haul in such a way. Extreme FEA analysis is carried-out to ensure product quality and technical conformity.